What is Porosity in Welding: Understanding Its Reasons and Enhancing Your Abilities
What is Porosity in Welding: Understanding Its Reasons and Enhancing Your Abilities
Blog Article
Porosity in Welding: Identifying Common Issues and Implementing Finest Practices for Avoidance
Porosity in welding is a pervasive concern that often goes undetected till it creates substantial issues with the integrity of welds. In this conversation, we will certainly discover the vital variables adding to porosity formation, examine its damaging impacts on weld performance, and talk about the finest practices that can be adopted to lessen porosity event in welding procedures.
Usual Reasons For Porosity
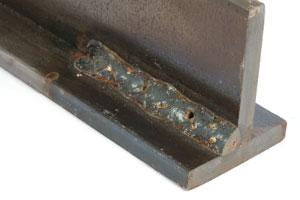
Utilizing dirty or wet filler materials can present pollutants into the weld, adding to porosity problems. To reduce these common reasons of porosity, complete cleaning of base metals, correct protecting gas selection, and adherence to optimal welding parameters are crucial techniques in accomplishing high-quality, porosity-free welds.
Influence of Porosity on Weld High Quality

The existence of porosity in welding can dramatically endanger the architectural integrity and mechanical homes of welded joints. Porosity develops spaces within the weld metal, compromising its total stamina and load-bearing capability. These gaps act as anxiety focus factors, making the weld extra at risk to breaking and failure under used tons. Additionally, porosity can lower the weld's resistance to corrosion and various other ecological elements, further decreasing its durability and efficiency.
Among the main repercussions of porosity is a decrease in the weld's ductility and toughness. Welds with high porosity degrees often tend to display lower influence toughness and minimized capability to warp plastically prior to fracturing. This can be especially concerning in applications where the bonded elements go discover this info here through dynamic or cyclic loading problems. Porosity can hinder the weld's ability to properly transfer pressures, leading to early weld failure and possible safety hazards in critical frameworks. What is Porosity.
Best Practices for Porosity Avoidance
To boost the structural honesty and top quality of bonded joints, what specific measures can be implemented to decrease the occurrence of porosity during the welding process? Utilizing the correct welding method for the particular product being bonded, such as readjusting the welding angle and weapon position, can additionally stop next page porosity. Routine assessment of welds and instant remediation of any problems identified during the welding process are vital methods to avoid porosity and produce top notch welds.
Importance of Correct Welding Strategies
Applying proper welding strategies is critical in guaranteeing the structural integrity and quality of welded joints, developing upon the foundation of efficient porosity prevention actions. Excessive warmth can lead to enhanced porosity due to the entrapment of gases in the weld swimming pool. In addition, using the proper welding criteria, such as voltage, current, and travel rate, is vital for attaining audio welds with marginal porosity.
Additionally, the selection of welding process, whether it be MIG, TIG, or stick welding, should straighten with the certain needs of the project to make sure optimum outcomes. Proper cleaning and preparation of the base metal, along with selecting the ideal filler product, are additionally essential components of proficient welding strategies. By sticking to these finest methods, welders can lessen the threat of porosity formation and create premium, structurally sound welds.
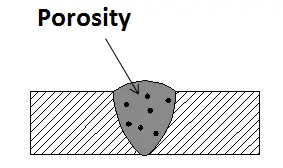
Evaluating and High Quality Control Actions
Testing treatments are necessary to find and protect against porosity in welding, making sure the strength and toughness of the last item. Non-destructive screening techniques such as ultrasonic testing, radiographic testing, and aesthetic inspection are frequently used to identify prospective issues like porosity.
Post-weld evaluations, on the various other hand, assess the final weld for any i loved this kind of problems, consisting of porosity, and validate that it meets specified requirements. Executing an extensive quality control plan that consists of detailed screening procedures and assessments is paramount to decreasing porosity concerns and ensuring the general high quality of bonded joints.
Verdict
In conclusion, porosity in welding can be a typical problem that impacts the top quality of welds. By determining the typical reasons of porosity and applying best techniques for prevention, such as appropriate welding strategies and screening measures, welders can guarantee excellent quality and trusted welds. It is important to prioritize prevention approaches to lessen the event of porosity and keep the stability of bonded structures.
Report this page